Modern Wire connector types in the Automotive Industry
Dive into the fascinating world of automotive wire connector types! In this section, you’ll learn about the basics of wire connectors, their vital role in vehicles, and how they’ve evolved through the ages. Journey with us through the riveting timeline of automotive history and the significant part played by these seemingly insignificant connectors.
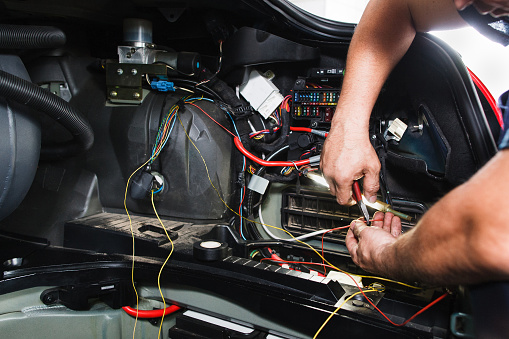
Basics of Wire Connectors
Different wire connector types are essential components in the electrical system of any vehicle. These tiny, yet significant elements form the bridge between different circuits, ensuring seamless transmission of electrical signals. Fundamentally, a wire connector includes male (plug) and female (socket) components. The design and structure of a connector depend on its application. For instance, connectors used for high-current applications often have larger pin sizes for maximum contact area. Material composition is another critical factor, with connectors often made from materials like copper, brass, or bronze, offering high conductivity and resistance to corrosion.
Importance and Functionality of Wire Connectors in Vehicles
Wire connector types in the automotive industry are far more critical than one might initially believe. These tiny components have a crucial role in relaying electrical signals across various vehicle systems, powering everything from the engine control unit to the radio in your car. The signals passed through these connector types enable the electronic components of your vehicle to communicate and function together, leading to a smooth driving experience. In the absence of effective wire connectors, the numerous electrical components within a car would not interact properly, leading to issues in performance and safety.
Evolution of Wire Connector types in Automotive History
The evolution of the various wire connector types in automotive history is a testament to technological progress. The first cars did not have many electrical components, therefore, complex wire connectors were unnecessary. As automobiles advanced and incorporated more electrical components, the demand for efficient and reliable connectors rose. Early connectors were simple and designed for specific tasks, with minimal interconnection between various systems. However, with the advent of electronic control units, GPS systems, electric windows, air conditioning, and more, the complexity of the various wire connector types increased. Modern vehicles now employ a vast array of connectors, each designed for a specific purpose and application, catering to the multitude of electronic systems present in today’s cars.
Different Wire Connector Types used in Automotive Industry
Ever wondered about the diverse wire connector types that keep your car running smoothly? From crimp connectors to Deutsch connectors, and much more, each has its unique attributes and applications. Join us as we unravel the intricacies of these connectors and their place in the automotive world.
Crimp Connectors
Crimp connectors are a commonly used wire connector type in automotive applications. They are named after the crimping process used to secure them to the wire. This involves compressing the connector onto the wire to form a secure mechanical and electrical bond. There are various types of crimp connectors:
Bullet Connectors
Bullet connectors are a type of crimp connector that is named after their shape. They consist of a male and a female component, which fit together like a plug and socket. This shape provides a secure connection, preventing the connectors from pulling apart easily. Bullet connectors are commonly used in applications where the connections may need to be disconnected and reconnected frequently, such as car audio systems.
Spade Terminals
Spade terminals, also known as spade connectors, are another type of crimp connector. They have a spade-shaped metal piece that is used to connect to a screw or stud. The spade shape allows for easy disconnection and reconnection without the need to completely remove the screw or stud. Spade terminals are commonly used in applications where the wire needs to be attached to a terminal block, such as in car stereo installations.
Butt Connectors
Butt connectors are used to connect two wires end-to-end, creating a straight-line connection. They are typically used when a wire needs to be extended, or when two different wires need to be connected together. The wires are inserted into each end of the butt connector and then crimped to form a secure connection. Butt connectors are often used in vehicle wiring repairs or installations.
Heat Shrink Connectors
Heat shrink connectors provide a durable and weather-resistant solution for connecting wires. They consist of a crimp connector enclosed in a heat-shrinkable tube. After crimping, heat is applied to the connector, causing the tube to shrink and tightly conform to the wires, providing a sealed and secure connection. These are particularly useful in environments where the connection may be exposed to moisture or other harsh conditions.
Weather Pack Connectors
Weather Pack connectors are specifically designed for outdoor and under-hood applications, offering excellent resistance to temperature, chemicals, and moisture. These connectors come in various configurations, accommodating from one to six terminals, making them ideal for automotive uses like engine management systems, where protection against the elements is necessary.
Deutsch Connectors
Deutsch connectors are high-quality, durable, and weather-resistant connectors frequently used in heavy-duty applications such as in commercial vehicles and machinery. They feature a unique seal design that keeps dirt, dust, moisture, and other elements out, ensuring reliable connections in harsh environments.Metri-Pack Connectors
Metri-Pack connectors are versatile, high-performance connectors designed for automotive applications that require optimal electrical performance, high-temperature durability, and robust designs. Metri-Pack connectors are often used in areas like fuel injectors, air conditioning systems, ABS, and other critical areas in a vehicle.
Molex Connectors
Molex connectors, named after the company that popularized them, are used widely in the automotive industry, known for their durability and versatility. They are available in a wide range of pin configurations and sizes, which can accommodate a variety of electrical applications.
USB Connectors
USB connectors are increasingly prevalent in modern vehicles, used for connecting mobile devices and other electronics for charging or data transfer. They offer a convenient, universal interface for various devices, enhancing the user experience in the vehicle.
Solder Connectors
Solder connectors are often used when a permanent, highly conductive connection is needed. They involve the use of solder, a metal alloy that melts to create a conductive bond between the wires and the connector. While providing excellent connectivity, the process requires skill and careful handling to avoid overheating and potential damage to the wire insulation.
Wire Connector Installation Techniques
Ever wanted to get hands-on with your vehicle’s wiring? Learn how wire connectors are installed using various techniques such as crimping, soldering, and heat shrinking. Each method has its unique benefits and uses. Dive in and empower yourself with practical automotive knowledge!
Crimping
Crimping is a popular method for installing wire connectors, often used in the automotive industry due to its relative simplicity and effectiveness. This process involves placing the stripped end of a wire into a connector, then using a special tool – the crimping tool – to deform the connector around the wire, creating a secure joint. The crimping process is both a mechanical and electrical bond, ensuring a reliable connection that can withstand vibration and movement often experienced in vehicles. It does not require any soldering or heat, making it a quick, easy, and efficient installation method.
Soldering
Soldering is a more traditional method for installing several wire connector types, especially when a strong, highly conductive, and permanent connection is required. It involves the use of a soldering iron to melt a metal alloy, known as solder, creating a bond between the wire and the connector. Soldering can provide excellent electrical connectivity and can ensure a long-lasting bond, but it does require careful handling and expertise to avoid damaging the wire or the connector.
Heat Shrinking
Heat shrinking is a process often used in conjunction with crimp or solder connectors. A heat shrink tube is placed over the connection and then heated, causing it to shrink down and tightly conform to the shape of the wire and connector. This creates a protective seal around the connection, providing additional mechanical strength and offering resistance against environmental factors such as moisture, dirt, and chemical exposure. The process is quick and efficient, but does require a heat source, often a heat gun or lighter, and careful handling to avoid overheating.
Q&A
Here we answer some of the most commonly asked questions about wire connector types:
What are some common problems encountered with automotive wire connector types?
Common problems include loose connections, corrosion, overheating, and wire breakage. These issues can cause intermittent electrical faults, poor performance, or even total failure of certain vehicle systems.
How can common wire connector issues be solved?
Solutions can range from simple to complex. For loose connections, reseating or replacing the connector might solve the problem. Corrosion can be treated with specific cleaning agents, while overheating might indicate a need for a connector with a higher current rating. Broken wires would need to be repaired or replaced.
What preventive measures can be taken to improve the durability of different wire connector types?
Regular inspection and cleaning can prevent buildup of dust and corrosion. Using connectors with adequate current ratings can prevent overheating. Additionally, proper installation techniques can prevent damage and ensure a secure connection.
When should wire connectors be replaced?
Wire connectors should be replaced when they show signs of damage, such as cracked or broken housing, burnt marks, or extensive corrosion. Also, if a connector is frequently causing issues, it may be best to replace it.
Why is proper maintenance of wire connectors important?
Proper maintenance ensures the longevity of wire connectors and their reliable performance. It prevents potential electrical failures that could affect the safety and efficiency of the vehicle’s operation. Regular checkups and appropriate upkeep can save on costly repairs or replacements in the long run.
Do you have any more questions? Join our Facebook community now to find what you’re looking for.